Natural
indigo dye produces a distinctive blue color that synthetic dyes simply cannot
replicate. Historically, this natural pigment is extracted from the leaves of
various plant species including wood, indigo, and polygonum. These plants
contain the greatest concentration of blue dye molecules, making them ideal to
use for the meticulous extraction process.
India
was the earliest major center for the production and processing of indigo dye.
The Indigo fera tinctoria species of the indigo plant was largely domesticated
in the country before the final product—which is the indigo dye—made its way to
the Romans and the Greeks, who valued it as a luxury. Of the three primary
colors, blue was considered the rarest and most regal mainly because it can
only be generated from a particular species of plant (unlike red and yellow,
which are easily derived from many kinds of flora and fauna).
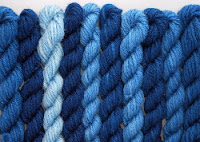
In
the early 1900s, over 30,000 acres of land were reserved for the cultivation of
Indigo, producing and shipping 4,000 tons of the natural blue dye per year.
Today, however, synthetic dyes are becoming more prevalent, pushing aside the
tradition that has been kept alive for hundreds of generations. Indigo farming
in India has since dwindled, leaving only one family currently engaged in the
trade. Fortunately, there are
companies that still support its legacy and tradition, keeping natural indigo
dye alive through their traditionally produced and designed shirts, sarees, and apparels.
Blog Source URL: https://www.studioenoy.com/blog/The-exciting-tale-of-indigo/